Patch Test Kits for Oil Analysis
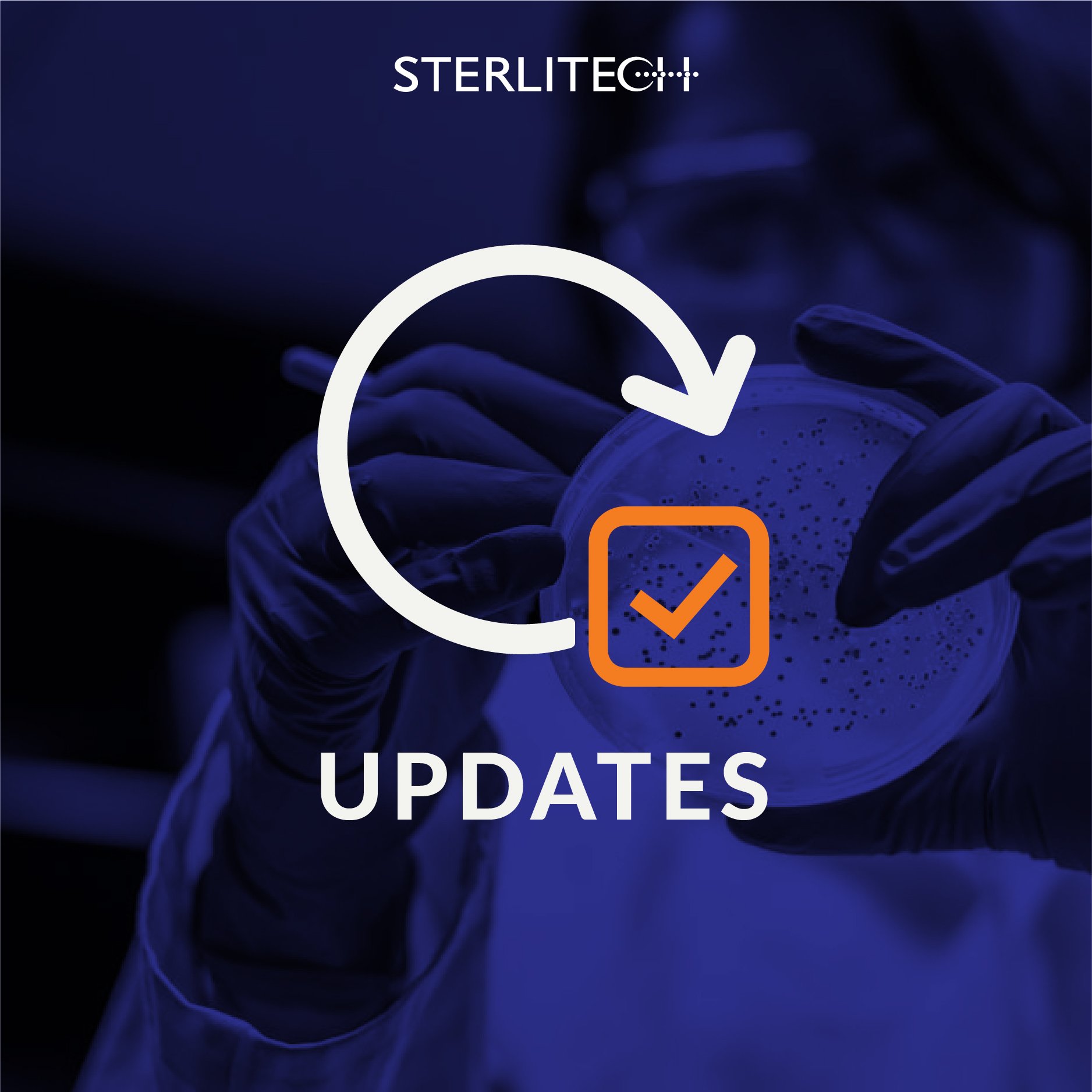
In order to keep costs down many companies perform in-house testing on the lubricating oil and hydraulic fluid in their machinery to monitor it for particulate contamination. While most facilities can’t match the detailed analysis that an oil analysis laboratory can provide, there are some commercially available kits out there that allow users to get a good idea about the quality of their industrial fluids instantly. This process is commonly known as a “patch test” and it includes the use of MCE filters to collect and isolate debris for evaluation (“patches” is a colloquial term for filters in the oil analysis industry). The ISO recognizes the important link between contaminated oils and component life and has published a cleanliness code as well as various standard methods, such as ISO 4406:1999, that testers can reference to determine how much particulate is acceptable. For the filtration aspect, our customers often use the sterile MCE membrane filters, which are individually wrapped and are actually less expensive than their non-sterile counterparts. Pore sizes and diameters vary by user; for a pore size larger than 1.2 micron a non-sterile MCE filter should be used (non-sterile MCE filters are available up to 8.0 microns). Clients performing this analysis can purchase the necessary components separately, but they often purchase a pre-assembled patch test kit which may include the filters, sample bottles, forceps, filter holder, a vacuum pump, and a visual correlation chart to compare the results to the approximate ISO cleanliness code. The actual components of the patch test kit, as well as the filter specifications, are likely to vary by provider so be sure to check out what is included in yours before ordering. Consult this article from Machinery Lubrication for more information on patch testing. Read ISO 4406:1999 Read “Decoding the ISO Cleanliness Code”
- Most Viewed Blog Articles (5)
- Company News (285)
- Emerging Technologies (64)
- Microbiology and Life Science News (93)
- Water and Fluid Separation News (97)
- Filtration Resources (93)
- Product News (19)